Gute Vorbereitung zahlt sich aus – informieren Sie sich über alle teilnehmenden Aussteller und das gesamte Produktspektrum, das auf der SPS präsentiert wird. Treffen Sie so gezielt die richtigen Geschäftspartner.
Auf dieser Seite finden Sie alle Aussteller der SPS 2025. Die Online-Ausstellersuche gibt Ihnen frühzeitig einen Überblick über die teilnehmenden Unternehmen und wird täglich aktualisiert.
Nutzen Sie die verschiedenen Filterfunktionen, um konkret nach Produktgruppen, Hallen u.v.m. zu suchen. Die Filter können auch beliebig miteinander kombiniert werden, so dass Sie die Suche ganz gezielt auf Ihre individuellen Kriterien anpassen können.
Aussteller der SPS 2025
SEW-EURODRIVE GmbH & Co KG
Über uns
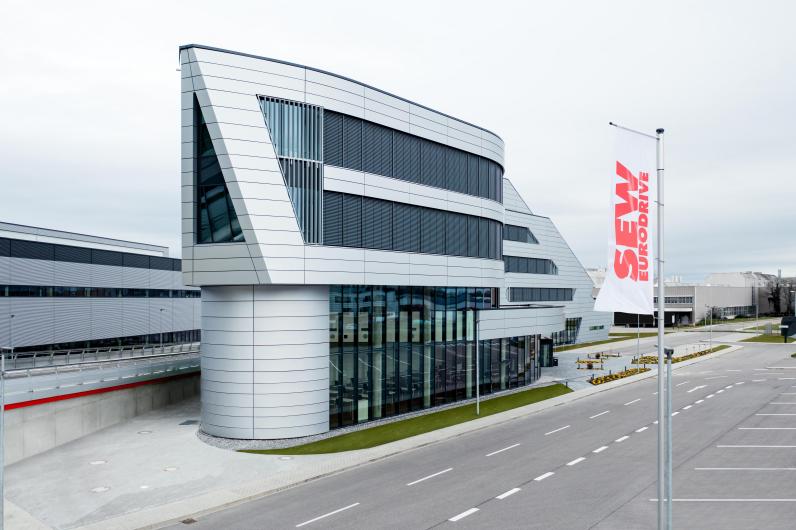
As one of the market leaders in drive and automation technology, SEW-EURODRIVE moves applications, processes, systems and machines in almost every industry. From fast, dynamic and high-precision, as in piece goods production, to large and powerful, as in the raw materials industry or in container terminals, to continuous and logistical processes, our solutions are at home all over the world. Countless conveyor belts, packaging machines, beverage bottling plants, logistics centres, gravel plants, cable cars, baggage carousels in airports and much more would come to a standstill without the drive technology and services offered by SEW-EURODRIVE.
With our more than 22,000 employees on all continents of the world, we not only play a key role in shaping the future of drive technology, but also that of our customers - and have been doing so for over 90 years. Since its foundation in 1931, SEW-EURODRIVE has been an owner-managed family business with headquarters in Bruchsal, not far from Karlsruhe, and generates sales of more than EUR 4.5 billion. With 17 production plants and 92 Drive Technology Centres in 57 countries, we are always close to our customers.
Unsere Produktgruppen
Keywords
- Steuerungstechnik
- Getriebe
- Frequenzumrichter
- Antriebstechnik
- Elektromotor
Unsere Produkte
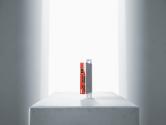
MOVI-C Controller
The new performance class progressive from the controller portfolio supplements the automation module set MOVI-C®. This high-performance, scalable motion and logic control solution makes it easy for mechanical and plant engineers to automate a whole range of applications. Three key market requirements for machine and system automation are met – scalability, smart technology and connectivity.
The MOVI-C CONTROLLER progressive is based on the new CPC (Cyber Physical Controller) modular system, which features numerous hardware components such as scalable CPU modules, fieldbus options (multi-protocol capability) and Wi-Fi variants. The passive cooling and RTC (Real Time Clock) function without battery replacement make 100% maintenance-free operation possible. The modular software system includes MOVIKIT® software modules, which meet every possible requirement in terms of motion control and real-time control, and solutions for safety, axis/controller replacement functions and configured code generation. By systematically implementing a software layer model based on Hypervisor technology, the new generation of controllers clearly sets itself apart from existing controller concepts on the market. This offers a simple means of enabling non-reactive interaction between the real-time controller on the one hand and, on the other, higher-level software functions such as visualization, condition monitoring, data mining, engineering software, diagnostics, IT communication stacks and intelligent sensors. A CFast memory card that supports extremely fast access to data enables the famously easy device replacement. The card contains all important data such as firmware, application, axis data sets and application data.
Due to its slimline design, the controller is also ideal for tight installation spaces . It can just as easily be used for modular machine modules as for coordinated tasks in a line network. Thanks to a cutting-edge software structure, the operating system is available separately and independently for engineering, programming, diagnostics and visualization. Version incompatibility issues between the individual programs are also a thing of the past. This solution enables simple operation and web visualization. HMI or OPC-UA enable visualization and external communication. The trend for hardware-independent solutions for machines is thus supported
Hardware designs: 1-core, 2-core, 4-core
4-core design feature: Real time (IEC Runtime) + Windows 10 IoT optional
Programming: CoDeSys 3, IEC61131-3
Fieldbus master: EtherCAT®/SBusPLUS
Fieldbus slave: EtherNet/IPTM, PROFINET IO, Modbus TCP, OPC UA
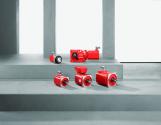
Servomotoren - Baureihe CM3C
SEW-EURODRIVE is adding servomotors for high external loads to the MOVI-C® modular automation system. The new CM3C series consists of the sizes 63, 71, 80, and 100. The motors have standstill torques from 2,7 to 40 Nm. This compact range of servomotors with increased inertia are used in machines and applications where a low ratio of load moment of inertia to motor moment of inertia is desired for control reasons. In addition, there is an extensive range of possible options, such as brakes, a large number of different encoder systems and encoder interfaces, as well as flexible motor connection variants for adapting perfectly to the respective conditions of the customer application. The new series is also optionally available with single-cable technology using the newly developed, SEW-EURODRIVE-internal MOVILINK® DDI encoder interface, making wide-ranging digital integration possible. For example, an automatic startup is performed when motors are connected to SEW-EURODRIVE inverters. The encoder signals are transmitted digitally and the brake control system is also digital, with an option for monitoring the condition of the brake. To provide customers with the greatest possible degree of flexibility in their system, the CM3C motor will be offered in future both with standard SEW-EURODRIVE encoder systems and also with DRIVE-CLiQ, EnDat 2.2, and HIPERFACE DSL® encoders. As is usual for SEW-EURODRIVE, the motor series offers a diverse range of options. When combined with the Bruchsal-based company's modular gear unit system, the possibilities are almost endless. One key unique selling point is the availability of two brake versions. Alongside the 24 V holding brake typical for servomotors, there is also a brake with increased working capacity for applications where service braking or emergency braking is required. In combination with the single-cable technology, there is also a new smart brake rectifier for the brake's AC connection. This is current-controlled and can cope with a wide range of input voltages from 100 to 500 V. Typical areas of application include machine automation, handling gantries, and trolley drives.
Sizes: 63, 71, 80, 100, each in the lengths S, M, and L
Rotational speeds: 2000, 3000, 4500, and 6000 min-1
Torque M0: 2.7 to 39.6 Nm
Maximum torque: 8.1 to 118.8 Nm
Inertia:1.54 to 99.5 kg/cm²
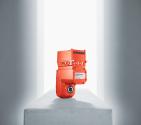
MOVIGEAR® performance
Within the modular automation module set MOVI-C® the mechatronic drive unit MOVIGEAR® performance is the first product for decentralized installation, consisting of parallel-shaft helical gear unit, permanent magnet motor and integrated drive electronics in a single housing.
MOVIGEAR® performance with direct fieldbus connection is intended especially for the area of dynamic materials handling technology and speed-controlled axes up to positioning tasks. Communication takes place via fieldbus interfaces, such as PROFINET IO, EtherNet/IP™ and Modbus TCP, and the integrated digital inputs and outputs.
The new drive unit is characterized by its compact design and high overload capacity. By achieving the highest motor efficiency class IE5 according to IEC TS 60034-30-2 and maximum system efficiency in accordance withto IEC 61800-9-2, MOVIGEAR® performance surpasses all conventional solutions to date.
These new products expand the possible applications of SEW‑EURODRIVE's decentralized drive technology, which has proven itself an asset over the decades. To combine its benefits with those of the MOVI‑C® modular automation system, the decentralized drive systems have been developed on the basis of the MOVI‑C® portfolio. They complement the products released so far in terms of functionality and consistency.
Typical areas of application for the new product portfolio include the food and beverage industry, intralogistics and parcel logistics, and also the automotive industry and airports.
Performance classes: 0.8 KW / 1.5 kW / 2.1 kW
Torque classes: 200 Nm / 400 Nm
Overload capacity: 300% for 5 s
Ambient temperature: -25 °C to +40 °C (+60 °C)
Degree of protection: IP65 according to EN 60529
Communication: PROFINET IO, EtherNet/IPTM, Modbus TCP, POWERLINK, EtherCAT®/SBusPLUS, AS-Interface, Binary Control,
Safety functions: Safe Torque Off (PL e) integrated
Encoder: Integrated multi-turn absolute encoder
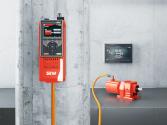
MOVITRAC advanced
Do you want to save time while also gaining flexibility? Now this is possible – with our MOVITRAC® advanced standard inverter. The unit can be used in a wide variety of areas of application thanks to its power range from 0.25 to 315 kW, as well as a comprehensive and scalable function package.
If you need a compact inverter that makes your work easier, but at the same time gives you openness with regard to control systems, our MOVITRAC® advanced standard inverter is the right choice.Designed and developed as a compact all-rounder, the MOVITRAC® advanced can control and monitor both synchronous and asynchronous AC motors with or without encoders, as well as asynchronous motors with LSPM technology or synchronous and asynchronous linear motors. It has a wide power range from 0.25 to 315 kW and an overload capacity of 150%.The MOVITRAC® advanced offers flexibilitythanks to its integrated communication interface which allows connection to commonly used control systems. It can be connected via PROFINET, EtherNet/IPTM, EtherCAT®/SBusPLUS, Modus TCP, EtherCAT® CiA402 or POWERLINK CiA402. You can also configure the functional safety with MOVITRAC® advanced – from the integrated safety function STO to higher-level safety functions and safe communication.The MOVITRAC® advanced is ideal for conveying and motion applications such as conveyor belts, hoists or palletizers – a truly compact all-rounder.
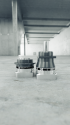
planetary gear unit
The new precision servo gear units PxG® were developed for use in a large variety of applications. They stand for top quality and technical innovation in the detail. A comprehensive modular system allows for the flexible adaptation regarding torque, gear ratio, output geometry or the interface to the servomotor. Exclusive individual elements such as the “Premium Sine Seal” oil seal, the use of SEW GearOil or the bearing system ensure a long service life, even under extreme loads.
From the modular system, three preferential series can be outlined as series of performance classes 5 to 7. Each series follows different requirements. Performance class 5 focuses on the use in dynamic motion sequences with a large number of acceleration and braking processes in intermittent duty. Performance class 6 is suitable for applications with high cyclic duration factor. A service life of 30,000 h can be achieved by modifying gearing and bearings as well as the use of a bellows coupling. The use of performance class 7 is optimal if space is at a premium. Maximum precision is achieved here already in the standard version by a rotational clearance of 1 to 2 angular minutes.
Innovative production and assembly processes ensure shortest delivery times and constant product quality. The relevant data of the final checks is attributed to the real product in the digital twin. Besides providing comprehensive documentation packages, this also enables improved simulation of the planetary gear units in the life cycle at a given gear unit utilization. The wear resistance reached in gearing secures operation through minimum deviations compared to the delivery state – even after many load cycles.
Due to the high positioning accuracy, typical areas of application are a large number of handling applications in the fields of robotics, automation and handling technology as well as machine tools and woodworking machines. The compact design and durability in continuous duty make these gear units ideal for use in food, packaging, printing, paper and textile machines.
Three series (performance classes 5 to 7)
Available sizes: 31, 41, 42, 51, 52
Output type: Solid shaft with/without key, flange block shaft and splining according to DIN5480
Nominal torque: 85 Nm to 600 Nm
Acceleration torque: 170 Nm to 820 Nm:
Rotational clearance: Standard 3 to 5 arcmin, reduced 1 to 3 arcmin
Service life: 20,000 h (P5, P6) and 30,000 h (P7)
Lubrication: Lubrication for life
Lubricant: SEW GearOil, food grade lubricants are available as alternative
Area of operation: -15 °C to +40 °C