Mit der Vorstellung des Journey 6P Domain Controllers von Horizon Robotics im April 2025 hat der Hightech-Konzern für KI-Chips und Computing-Plattformen einen wichtigen Impuls für modulare Antriebssysteme gesetzt: Das innovative, steckbare Design ermöglicht es, die Rechenplattform für intelligente Fahrfunktionen im Fahrzeug ähnlich flexibel wie einen PC aufzurüsten – ohne aufwendige Umbauten oder Komplettaustausch der Hardware. Diese Modularität eröffnet nicht nur Automobilherstellern, sondern auch Branchen wie der Automatisierungstechnik Möglichkeiten, aktuelle und künftige Anforderungen an intelligente Antriebe effizient und nachhaltig zu erfüllen.
Denn auch die Automatisierung steht vor einem Paradigmenwechsel: Immer kürzere Produktlebenszyklen, steigende Anforderungen an Energieeffizienz und die Notwendigkeit, Maschinen schnell an neue Aufgaben anzupassen, erfordern Antriebslösungen, die sowohl mechanisch als auch softwaretechnisch wandlungsfähig sind. Traditionelle Antriebssysteme, die als starre Einheiten konzipiert sind, stoßen hier an Grenzen – sei es durch hohen Engineering-Aufwand, lange Umrüstzeiten oder begrenzte Skalierbarkeit. Diese Herausforderungen haben die Entwicklung modularer Antriebe und Drive Intelligence vorangetrieben, zwei Konzepte, die heute als Schlüssel für agile und zukunftssichere Automatisierungslösungen gelten.
Modularität und Intelligenz sind entscheidend
Moderne Produktionsumgebungen müssen nicht nur präzise, sondern auch extrem flexibel sein. Einerseits treiben Themen wie Individualisierung (Stichwort „Losgröße 1“) und dezentrale Fertigung die Nachfrage nach Maschinen, die sich schnell umkonfigurieren lassen. Andererseits erfordern Nachhaltigkeitsziele energieeffiziente Systeme, die ihren Zustand eigenständig überwachen und optimieren können. Herkömmliche Antriebe, bei denen Motor, Getriebe und Steuerung als separate Komponenten installiert werden, sind hier oft zu unflexibel: Jede Änderung an der Kinematik oder Anwendung erfordert aufwendige Neuplanung und manuelle Anpassungen.
Hinzu kommt die zunehmende Vernetzung in Industrie-4.0-Umgebungen. Antriebe müssen heute nicht nur Bewegungen ausführen, sondern auch Daten liefern, die für Predictive Maintenance, Prozessoptimierung oder die Integration in übergeordnete IT-Systeme genutzt werden. Diese Anforderungen haben zur Entwicklung modularer Antriebe geführt, die sich wie Baukästen kombinieren lassen und Drive Intelligence, die diese Module mit softwarebasierten „smarten“ Funktionen ausstattet.
Modul-Kombinationen ermöglichen maßgeschneiderte Antriebsstränge
Modulare Antriebe sind als eigenständige, standardisierte Einheiten konzipiert, die je nach Anwendung zu komplexen Systemen zusammengesetzt werden können. Jedes Modul umfasst typischerweise:
- Mechanische Komponenten: Motor, Getriebe und ggf. Bremse in kompakter Bauform
- Elektronik: Integrierte Leistungselektronik und Steuerungsfunktionen
- Schnittstellen: Standardisierte Anschlüsse für Stromversorgung, Kommunikation und Medien (Daten, Luft, Hydraulik)
Das Prinzip ähnelt Lego-Steinen: Durch die Kombination verschiedener Module – etwa für lineare oder rotatorische Bewegungen, unterschiedliche Drehmomente oder Geschwindigkeiten – entstehen maßgeschneiderte Antriebsstränge. Ein Beispiel ist das Atro-System von Beckhoff, bei dem Motormodule in I- oder L-Form mit passiven Verbindungselementen zu Robotern mit bis zu sieben Achsen kombiniert werden. Jedes Modul enthält dabei bereits die komplette Antriebselektronik, was den Verdrahtungsaufwand minimiert und dezentrale Steuerungsarchitekturen ermöglicht.
Mit Drive Intelligence lernen Antriebe
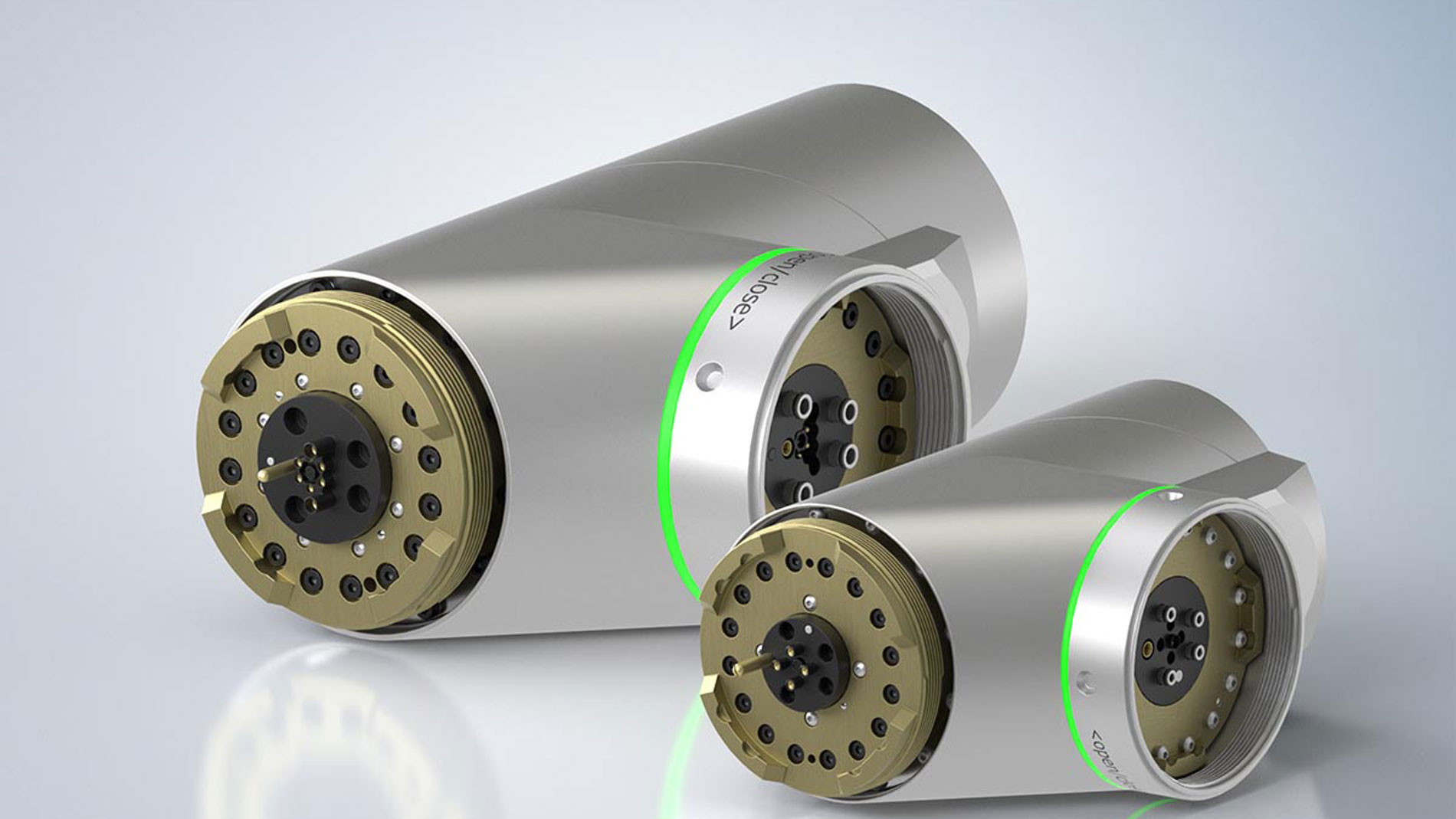
Drive Intelligence ergänzt die mechanische Modularität durch softwarebasierte Intelligenz. Dabei handelt es sich um die Integration von:
- Sensorik: Encoder, Drehmomentsensoren und Temperaturfühler erfassen Echtzeitdaten.
- Steuerungsalgorithmen: Adaptive Regelungstechniken passen die Antriebsparameter dynamisch an Laständerungen an.
- Kommunikationsfähigkeiten: Schnittstellen wie OPC UA oder EtherCAT ermöglichen die Anbindung an IoT-Plattformen.
- KI-Funktionen: Maschinelles Lernen optimiert Energieverbrauch oder erkennt Anomalien im Betrieb.
Das Atro-System von Beckhoff ermöglicht den Aufbau von Robotern mit modularen Motormodulen in I- oder L-Form. Diese Module bilden ein vollständiges Antriebssystem für jede Roboterachse. Bild: Beckhoff
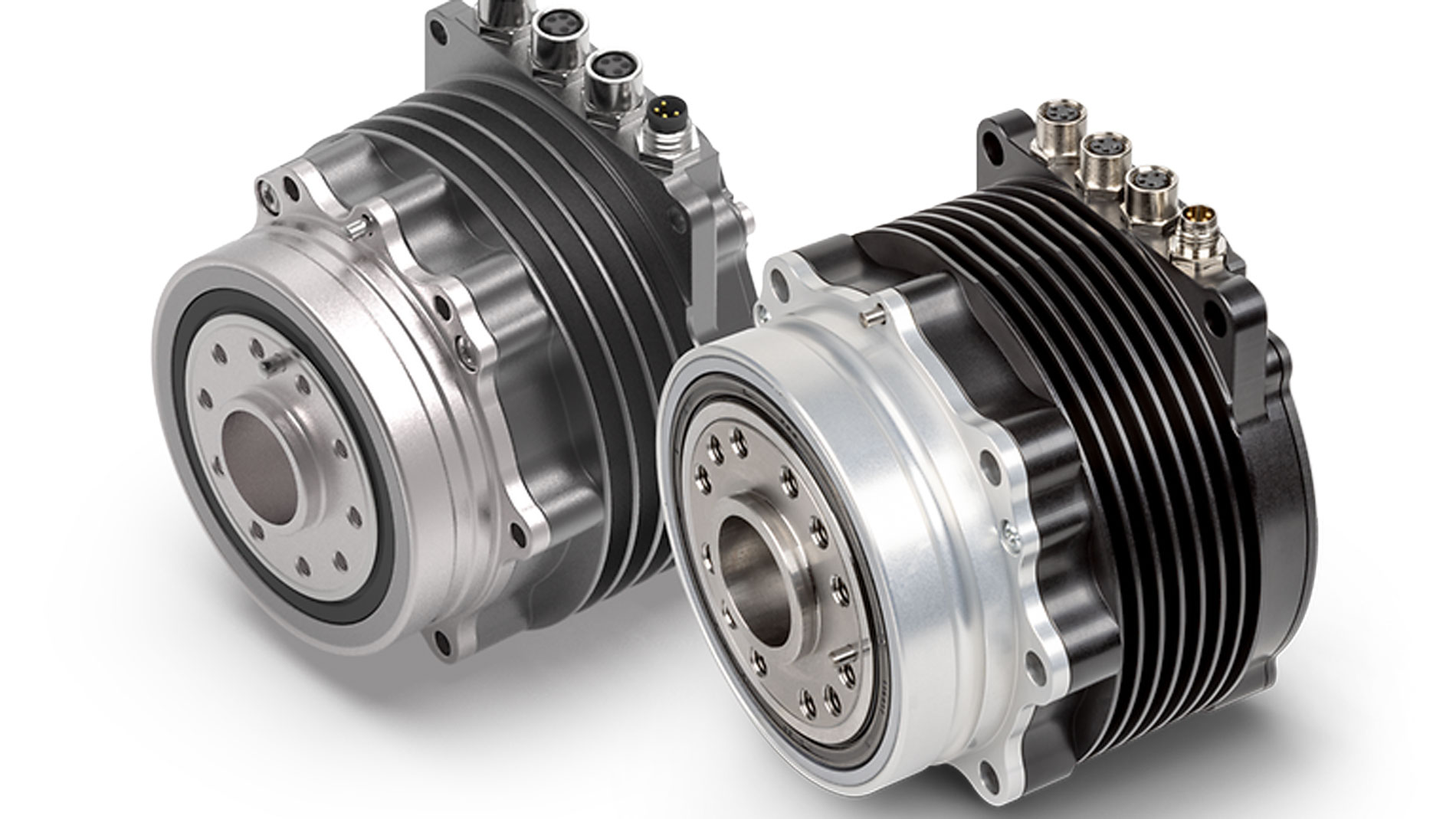
Die Skalierbarkeit modularer Antriebskonzepte bildet die Grundlage dafür, dass intelligente Funktionen wie Lastverteilung oder die Synchronisation mehrerer Achsen besonders effizient umgesetzt werden können. Diese enge Verzahnung von Modularität und Drive Intelligence zeigt sich bei Lösungen, die auf hochintegrierte, flexibel kombinierbare Systeme setzen. Ein Beispiel ist das Drive-Systems-Portfolio von Maxon. Maxon bietet mit seinen High Efficiency Joint Modules und High Precision Joint Modules vollständig integrierte Antriebseinheiten, die Motor, Getriebe, Elektronik und Sensorik in einem kompakten Modul vereinen. Diese Module sind speziell für den flexiblen Aufbau von Robotergelenken konzipiert, lassen sich leicht kombinieren und ermöglichen so maßgeschneiderte Roboterkinematiken für verschiedenste Anwendungen – von humanoiden Robotern bis zu mobilen Manipulatoren. Die integrierte Elektronik und die Unterstützung moderner Kommunikationsstandards wie EtherCAT reduzieren den Verdrahtungsaufwand und erleichtern die dezentrale Steuerung.
Der chinesische Hersteller Veichi präsentierte auf der SPS 2024 den SD710-Servoantrieb, der sich durch kompakte Abmessungen und integrierte Buskommunikation (EtherCAT, CANopen) auszeichnet. Die Drive Intelligence liegt hier in der automatischen Parameteranpassung: Ein KI-Algorithmus analysiert die mechanische Last und optimiert die Regelungsparameter ohne manuelle Eingriffe.
Die High Efficiency Joint Modules und High Precision Joint Modules von Maxon sind integrierte Antriebseinheiten, die Motor, Getriebe, Elektronik und Sensorik vereinen, sich leicht kombinieren lassen und so maßgeschneiderte Kinematiken ermöglichen. Bild: Maxon
Gesundheit des Antriebs visualisieren
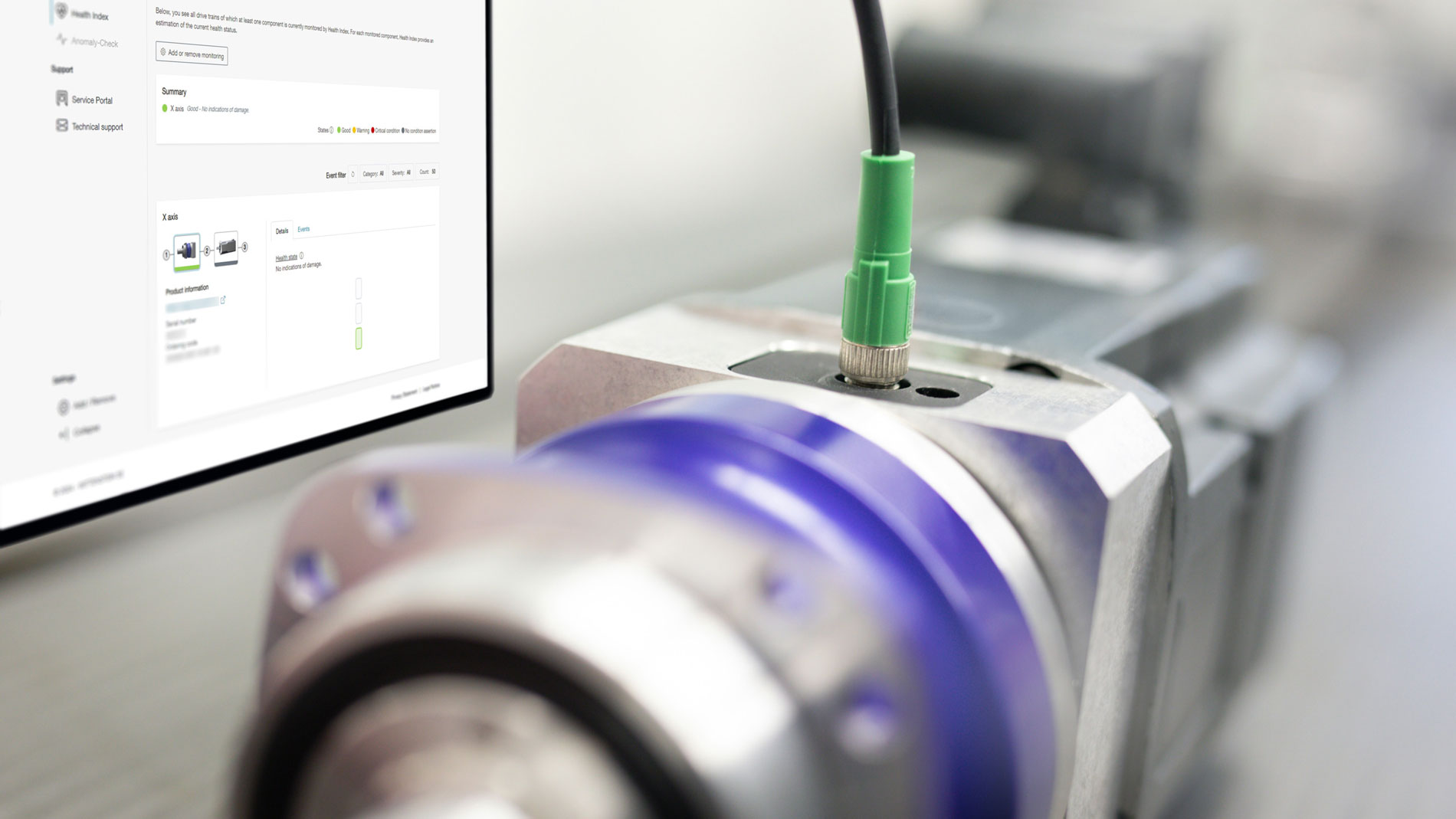
Der Health Index von Wittenstein ist ein digitales Tool, das über integrierte Sensorik und KI-gestützte Algorithmen Zustandsdaten wie Vibration, Temperatur und Verschleiß von Antriebssträngen erfasst, analysiert und den „Gesundheitszustand“ der Komponenten in einer Ampelfunktion visualisiert. Durch die Echtzeitauswertung von Betriebsdaten wie Drehmoment und Drehzahl können Anwender frühzeitig kritische Zustände erkennen und gezielte Handlungsempfehlungen für Wartungsintervalle oder den Getriebeaustausch ableiten. Diese prädiktive Überwachung reduziert ungeplante Stillstände und senkt Ausfallkosten, während vorkonfigurierte Module den Engineering-Aufwand minimieren und die Time-to-Market verkürzen. Die Standardisierung der Antriebskomponenten führt zudem zu geringeren Lagerhaltungskosten, und energieoptimierte Algorithmen tragen durch effizientere Betriebsweisen zur Reduktion des CO₂-Fußabdrucks bei. Durch die Integration in Industrie-4.0-Plattformen wie ctrlX Automation von Bosch Rexroth ermöglicht das Tool zukunftssichere Updates, die neue Funktionen oder erweiterte Analysemodelle nachrüstbar machen – ohne Hardwareänderungen.
Vielversprechend ist auch die Kombination modularer Antriebe mit Energy Harvesting: Module können Bremsenergie rückgewinnen oder über integrierte Piezo-Elemente Strom aus Vibrationen erzeugen – mehr zu diesem Thema in der Meldung „Energierückgewinnung in der Antriebstechnik“, ebenfalls in diesem Newsletter. (hjs)
Das Health-Index-Analysetool von Wittenstein erfasst und überprüft funktions- und belastungsrelevante Daten von Antriebssträngen in der Anwendung – und bietet so die Möglichkeit, kritische Betriebszustände und damit verbundene Ausfallrisiken frühzeitig zu erkennen. Bild: Wittenstein SE