Gute Vorbereitung zahlt sich aus – informieren Sie sich über alle teilnehmenden Aussteller und das gesamte Produktspektrum, das auf der SPS präsentiert wird. Treffen Sie so gezielt die richtigen Geschäftspartner.
Auf dieser Seite finden Sie alle Aussteller der SPS 2025. Die Online-Ausstellersuche gibt Ihnen frühzeitig einen Überblick über die teilnehmenden Unternehmen und wird täglich aktualisiert.
Nutzen Sie die verschiedenen Filterfunktionen, um konkret nach Produktgruppen, Hallen u.v.m. zu suchen. Die Filter können auch beliebig miteinander kombiniert werden, so dass Sie die Suche ganz gezielt auf Ihre individuellen Kriterien anpassen können.
Aussteller der SPS 2025
TR Electronic GmbH
Über uns
We provide: measurement and control systems for automation technology When industrial processes run smoothly and reliably, there are chances that this is partly due to measurement and control solutions from TR-Electronic. When a theater curtain goes up, for example, systems of TR monitor the complex stage technology. People and machines work safely together and the audience enjoys a perfect production. Wind energy plants generate energy with maximum efficiency thanks to optimally aligned rotor blades - controlled by TR solutions. In press lines for the automotive industry, TR sensors guarantee safe forming of the body components. In logistics, TR measuring systems enable smooth transport of goods, e.g. in conveying systems and high racks. TR control and measuring modules control and monitor pumps for drinking water supply, regulate correct feeding of pellets in wood-fueled installations or help to detect faults in a punching machine at an early stage. For all of these and other applications TR-Electronic supplies the right rotary encoders, linear encoders and drives – as high-quality standard products or customized solutions.
TR-Electronic develops, manufactures and sells sensors and actuators for industrial applications in automation technology. In order to better integrate the individual competencies and make them more transparent for our customers, we have organized the company into business units: Products in the Rotary Encoders Business Unit with optical or magnetic scanning are required to detect the angular movement of a rotating shaft. Magnetostrictive linear encoders measure the position of a linear movement without contact, for example in a hydraulic cylinder. Intelligent compact drives from the Motion Business Unit are used as actuators or, in the high-end version, as process drives. Customized control and measuring modules in combination with special know-how in pressing and punching processes complete the extensive product portfolio. Automation components from the Components Business Unit complete the product range. The development services provided by the Automation Business Unit bring press lines to new levels of performance, provide smart metering solutions for efficient energy utilization and fair billing, enable remote monitoring of water supply networks or ensure a cozy environment through intelligent heating automation.
Keywords
- SIL3, PLe
- Sicherheitsdrehgeber
- Dezentrale Stellantriebe
- Functional Safety
- Absolutdrehgeber
Unsere Produkte
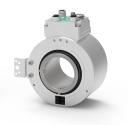
Precise acquisition of rotation angle of large hollow shafts
C_H1102 absolute rotary encoder with "all" interfaces
When transferring high torques or for shafts that contain lines and media hoses, large shaft diameters are required. Decoupling of the movement is not always possible for a rotary encoder with a traditional coupling using a second shaft end. In this case the rotary encoder must be large enough to take the drive shaft. The C_H1102 absolute multiturn encoders take shafts up to 50 mm in diameter, making them an excellent choice for these tasks in heavy machinery construction, machine tool manufacturing and wireless technology. With a resolution per revolution of 15 or 18 bits and 256000 absolute scanned revolutions, C_H1102 encoders offer high precision combined with a large measuring range.
The output value can be converted using fractional scaling factors. Thus a smooth measuring range transition is also achieved with rotary axes, without a rounding error developing.
If the rotary encoder is mounted so that it is seated on the shaft, it is very tolerant with regard to eccentricity of the shaft, which can occur with large, powerful drives. The bearings of the encoder carry only the encoder's own weight. Uneven running of the shaft thus has little influence on the service life of the rotary encoder. A groove/pin connection or a spring steel torque support secures the encoder against rotation.
The modular design of the latest series of rotary encoders from TR-Electronic means that the C_H1102 can be equipped with all the interfaces available for the smaller TR 582 and 802 series. The spectrum extends from IO-Link and classic field buses through to the widely used Industrial Ethernet PROFINET, EtherCAT, Ethernet/IP and also includes interfaces like INTERBUS and DRIVECLiQ.
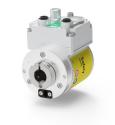
Compact absolute encoder for SIL3 applications with Industrial Ethernet or CAN
CD_582+FS Ethernet/IP – CIPsafety made by TR-Electronic
- SIL3 / SIL 2
- CIPsafety over Ethernet/IP, PROFIsafe over PROFIBUS, open Safety over Ethernet Powerlink; CANopen safety
- Redundant layout (KAT4): two fully independent multiturn absolute encoders in the size of a single one
- Incremental output as an option (HTL, TTL, sincos)
- Most current profiles available in Industrial Ethernet
Absolute rotary encoder in standard dimensions of 58mm holds a true absolute multi-turn double rotary encoder system with integrated safety evaluation. Secured position data (“Safe Position” – SLP) are transmitted via secured bus system to the safety controller. Depending on safety requirement of the specific applications, CD_582+FS fulfil maximum safety standard SIL3, PLe. They are available as well in an optimized version to meet SIL2, PLd requirements.
CD_582 uses the standard modular system of “Generation 2” absolute shaft encoders designed by TR-Electronic. For solid shaft, keyway and key provide the form closure required for reliable connection between application and encoder. The same purpose fulfill partial keyways in blind and hollow shaft encoders with up to 15 mm diameter. Almost any installation situation can be implemented with the standard flange variants. With solid and blind shafts, the user has additional choice placing the connectors at the side of the encoder or at the back side (opposite to the shaft). With limited mounting space, this choice can help to safe some cm.
CD_582+FS are capable of preset adjustment (referencing) in full operation even with moving axis.
The CD_582+FS can be applied in accordance with the current basic and execution standards to an axis, a system module, or a machine with safety functions wherever a standard 58 mm shaft encoder has been used. In principle, the CD_582+FS fits wherever the non-functionally safe CE_582 and CM_582 could be installed. With CD_582+FS, safe and secured automation is no more a matter of installation space.
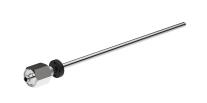
Linear absolute position measuring systems
Linear position measuring systems based on magnetostriction detect the position of moving machine parts without contact and thus wear-free in many applications.
Currently TR-Electronic offers the high-end solution LM_I 46 with resolutions of 0.001 mm, which can be equipped with Industrial Ethernet. And LM_B 48 cost-effectively supplies simple applications with a measuring range of 2.5 m and a resolution of 0.1 mm.
The new series LM_S 34 closes the gap between these two devices. The first family member is the sensor rod LMRS 34 for direct installation in hydraulic cylinders. Measuring lengths of up to 3 m are supplied with the common direct linear sensor interfaces SSI, Analogue, and CAN. LMRS 34 achieves a resolution of 0.01 mm. The head’s width across flats is 34 mm, hence the size designation “34”. This is noticeably smaller than the 48 mm or 46 mm of the other families and is undercut only by the ultra compact LMRB 27. However, it requires an external converter box for all interfaces except Analogue.
LMRS 34 offers a very compact sensor solution in the middle range that can be equipped with the most important interfaces. LMRS 34 works completely wear-free as does every magnetostriction measuring system from TR-Electronic. The stainless steel casing is pressure tested. The screw thread fits into many standard cylinders. All ring, half-round, float and block magnets available from TR-Electronic can be used with LMRS 34 to install the measuring system in a hydraulic cylinder, for level measurements or in a machine with an open tube as a normal position sensor.
LMRS 34 is also available with IO link interface for accessing further areas of application. LMRS 34 can internally monitor positions and ranges and derive the state of the initiator-compatible digital output. For instance, this enables simple level monitoring using digital signals. The fill level is also available to a corresponding controller as a continuous measurement signal via IO link.
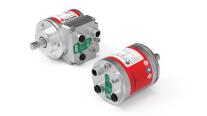
C__582 Rotary encoder: small, flexible, fast
Everything the application needs – reduce to the max.
- High precision optical: 15 bit / turn, 18 bit / turn
- Robust magnetic: 13 bit / turn
- Up to 4,096 absolutely scanned per revolution
- Versatile networker as standard
- Supports modern Industrial Ethernet variants: PROFInet, EtherCAT, Ethernet/IP, Powerlink
- Industrial fieldbuses: CANopen, PROFIbus, Interbus
- Point-to-Point: SSI, analog, parallel, RS485, IO-Link, DRIVECLIQ
- Solid shaft, blind shaft, hollow shaft, draw-wire mechanics, claw coupling
- Protection class up to IP67
- Connectors axial or radial
- Gear parameters given as fraction (numerator / denominator) for repeating rotary axes without rounding error
- Synchronized detection for highly performant position control
- Latest communication standards for Industry 4.0
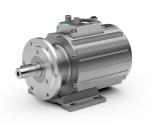
Heavy-duty multi-turn encoder with approval up to SIL3 / PLe
The functionally safe absolute multi-turn encoders by TR-Electronic CD_75 are established in the market. Stainless steel and ATEX versions open up new fields of application. A collar bearing that is integrated in the safety assessment will absorb large shaft forces. TR-Electronic GmbH has developed another version for crane systems in the steel industry: CDV115M+FS. Built into the tried-and-tested heavy-duty housing of the 115 series, SIL3 absolute encoders can be used for the entire shaft encoder even when high mechanical loads occur, such as those encountered in container loading cranes in port facilities or in the steel industry. Solid shafts up to 20 mm in diameter are available and properly dimensioned tongue-and-groove joints ensure an adequate engagement. The generously dimensioned bearing absorbs large shaft forces. The heavy-duty housing protects the encoder so that it can withstand rough handling, such as when misused as a passenger hoist or when knocked against other logistics vehicles. The condensation proof double magnetic sampling provides an IP65 rating and a temperature range of -40 to +65 °C. Saved absolute position and velocity values are transmitted via PROFIBUS, PROFINET (with PROFIsafe protocol), EtherCAT (according to the Standard Functional safety over Ethercat) or Powerlink (with OPENsafety protocol). Measured values are also available via unsecured protocols for faster signal processing. The secure protocol parts also serve for monitoring position and speed ranges. Fast actual values can be used for real-time enabled position control. Both from one and the same encoder system. The diverse redundant combination of glass and magnetic scanning provides incremental signals for the local speed feedback of a frequency converter. Thus, CDV115M assumes the function of up to three separately mounted encoders: Secured position and speed values, real-time enabled position and speed for central control and speed feedback for local control. And the robust protective housing enables all these functions to be performed where no conventional encoder would last long.