Condition Monitoring und Predictive Maintenance sind zentrale Bausteine der digitalen Transformation in der Industrie. Sie stehen exemplarisch für die zunehmende Vernetzung von IT und OT und ermöglichen es, Produktionsanlagen und Maschinen effizienter, zuverlässiger und kostengünstiger zu betreiben. Während Condition Monitoring die kontinuierliche Überwachung des Anlagenzustands beschreibt, geht Predictive Maintenance einen Schritt weiter: Durch die intelligente Auswertung von Sensordaten lassen sich Wartungsbedarfe vorausschauend erkennen und gezielt planen – ein Paradigmenwechsel gegenüber der klassischen, intervallbasierten Instandhaltung.
Die Vorteile liegen auf der Hand: Ungeplante Stillstände werden vermieden, Ausfallzeiten minimiert und defekte Komponenten können frühzeitig erkannt und ersetzt werden. Wartungsarbeiten lassen sich kostenoptimal terminieren, was nicht nur die Produktionskosten senkt, sondern auch die Energieeffizienz steigert. Die Marktentwicklung unterstreicht die Relevanz: Laut einer Studie von Future Market Insights wird der globale Markt für Condition Monitoring bis 2034 auf 6,19 Milliarden US-Dollar anwachsen. Treiber dieser Entwicklung sind technologische Fortschritte in der Sensorik, leistungsfähigere Datenanalysen und die verstärkte Integration mit IIoT-Plattformen. Unternehmen, die auf diese Technologien setzen, berichten von signifikanten Einsparungen: So lassen sich die Wartungskosten um bis zu 40 Prozent reduzieren, die Lebensdauer von Anlagen verlängern und die Maschinenverfügbarkeit um bis zu 30 Prozent steigern.
Die wirtschaftlichen Vorteile ergeben sich aus mehreren Faktoren. Durch die kontinuierliche Überwachung des Anlagenzustands können Wartungsarbeiten gezielt und bedarfsgerecht durchgeführt werden, anstatt nach starren Intervallen oder erst im Schadensfall zu reagieren. Dies minimiert ungeplante Stillstände, reduziert den Aufwand für Notfallreparaturen und senkt die Kosten für Ersatzteile und Arbeitszeit. Gleichzeitig wird die Produktivität gesteigert, da die Anlagenverfügbarkeit steigt und Produktionsausfälle seltener werden. Die frühzeitige Erkennung von Verschleiß oder Fehlfunktionen ermöglicht es, Komponenten rechtzeitig auszutauschen und so die Lebensdauer der Maschinen zu verlängern. Dies wirkt sich nicht nur positiv auf die Investitionskosten aus, sondern trägt auch zur Nachhaltigkeit bei, da Ressourcen effizienter genutzt werden.
Ein weiterer Aspekt ist die verbesserte Planungssicherheit: Predictive Maintenance liefert datenbasierte Prognosen über den Zustand und die verbleibende Lebensdauer von Anlagen. Unternehmen können so Wartungsmaßnahmen optimal terminieren, Ersatzteile rechtzeitig beschaffen und Personalressourcen effizient einsetzen. Die Integration von Condition Monitoring in IIoT-Plattformen eröffnet zudem neue Möglichkeiten für die Automatisierung und Fernüberwachung, was insbesondere für global agierende Unternehmen mit verteilten Produktionsstandorten von Vorteil ist. Die gesammelten Daten dienen nicht nur der Instandhaltung, sondern liefern auch wertvolle Erkenntnisse für die Prozessoptimierung und das Energiemanagement.
Die Investition in Condition Monitoring und Predictive Maintenance zahlt sich somit auf mehreren Ebenen aus: Sie steigert die Wettbewerbsfähigkeit, erhöht die Betriebssicherheit und unterstützt Unternehmen dabei, den steigenden Anforderungen an Effizienz, Nachhaltigkeit und Digitalisierung gerecht zu werden.
Ein Blick in die Praxis zeigt, wie vielfältig die Lösungen inzwischen sind. Moderne Condition Monitoring Systeme setzen auf eine breite Palette von Sensoren, die Schwingungen, Temperaturen, Drücke oder Füllstände erfassen. Besonders bei rotierenden Maschinen wie Motoren, Pumpen oder Getrieben ist die Schwingungsüberwachung essenziell, da sie frühzeitig auf Verschleiß oder Unwuchten hinweist. Temperaturmessungen an kritischen Komponenten wie Lagern oder Spindeln liefern zusätzliche Indikatoren für drohende Ausfälle. Die Integration dieser Sensoren in bestehende Automatisierungsstrukturen erfolgt heute meist über standardisierte Schnittstellen wie IO-Link, was die Anbindung an übergeordnete IT-Systeme erleichtert.
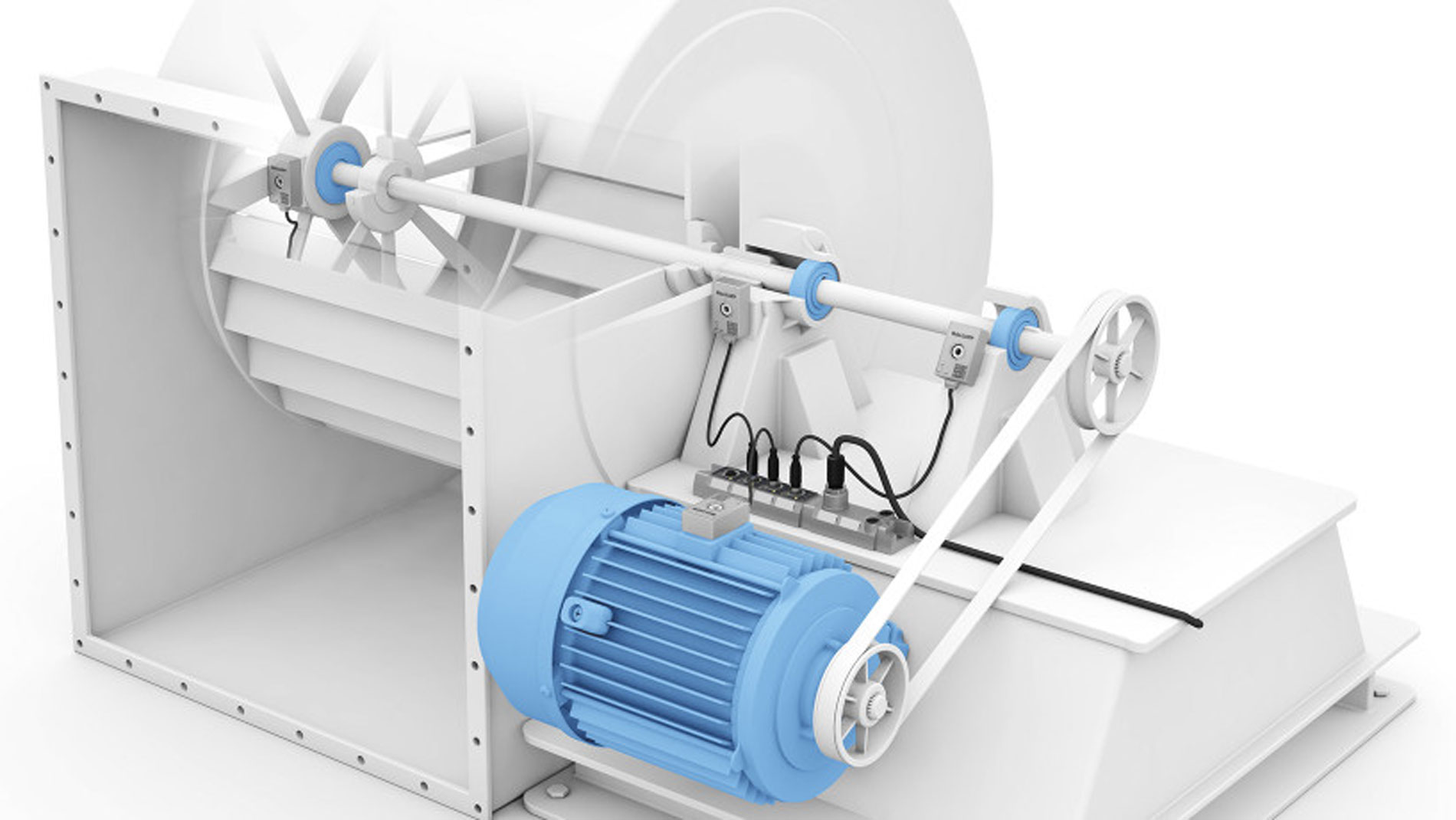
Ein Beispiel für die technologische Weiterentwicklung ist der BCM Condition Monitoring Sensor von Balluff, der in seiner zweiten Generation nicht nur Vibrationen, Temperaturen, Feuchtigkeit und Luftdruck misst, sondern auch die Daten direkt im Sensor vorverarbeitet. Mithilfe von Algorithmen wie der schnellen Fourier-Transformation werden Schadensfrequenzen erkannt und Alarme ausgelöst, lange bevor ein Schaden hör- oder sichtbar wird. Die Datenmenge wird dabei durch die Vorverarbeitung drastisch reduziert, was die Übertragung und Analyse in der IT-Infrastruktur vereinfacht. Die Konfiguration solcher Systeme ist mittlerweile so intuitiv, dass auch Anwender ohne tiefgehende IT- oder Schwingungsanalysekenntnisse professionelle Zustandsüberwachung implementieren können.
Ungeplante Stillstände und Störungen im Produktionsprozess lassen sich mit den BCM Condition Monitoring Sensoren von Balluff effizient vermeiden: Die intelligenten Sensoren liefern Zustandsdaten, mit denen kostenintensive manuelle Inspektionen automatisiert werden können. (Bild: Balluff))
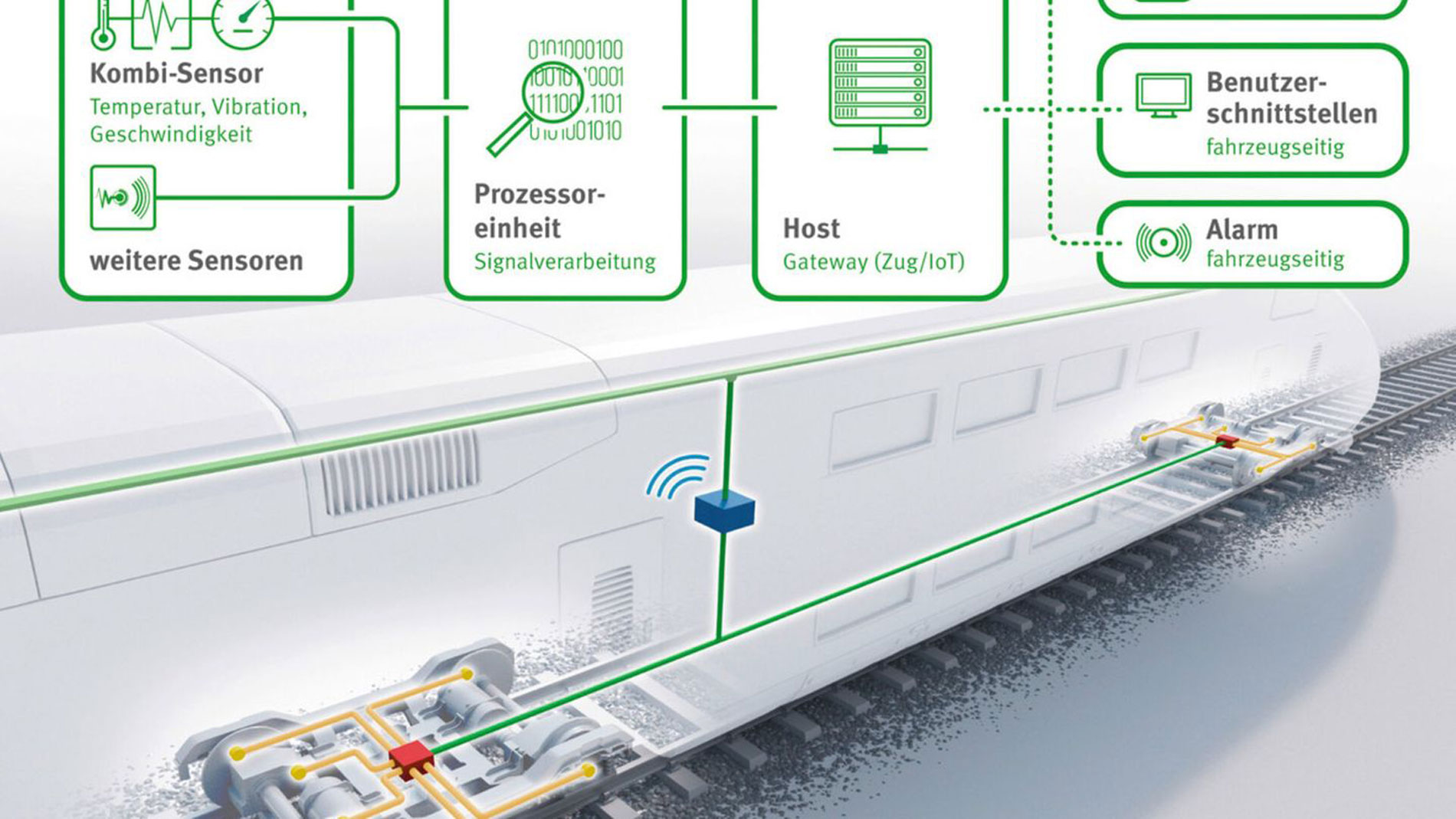
Auch im Bereich der Schienenfahrzeuge zeigt sich, wie Condition Monitoring und Predictive Maintenance die Verfügbarkeit und Sicherheit erhöhen. Schaeffler etwa hat ein Onboard Condition Monitoring System entwickelt, das sowohl cloudbasiert als auch lokal betrieben werden kann. Kombisensoren erfassen Schwingungen, Temperaturen und Drehzahlen an Trieb- und Laufdrehgestellen und übertragen die Daten an einen Onboard-Server. Die Analyse erfolgt über Prozessmodule, die als Schnittstelle zum übergeordneten Zugsystem dienen. Besonders innovativ ist der Einsatz von akustischen Kameras im Rahmen des Acoustic Thermal Management Systems (ATMS), das Geräusche entlang des Fahrwegs aufnimmt und daraus in Echtzeit Schallintensitätskarten erstellt. So können Fehlerdiagnosen und Trendanalysen mit einer Vorwarnzeit von bis zu einer Woche erstellt werden – ein deutlicher Fortschritt gegenüber klassischen Heißläuferortungsanlagen.
Das Schaeffler Railway Condition Monitoring System ermöglicht die vorausschauende Zustandsüberwachung von kompletten Trieb- beziehungsweise Laufdrehgestellen in Personenzügen. (Grafik: Schaeffler)
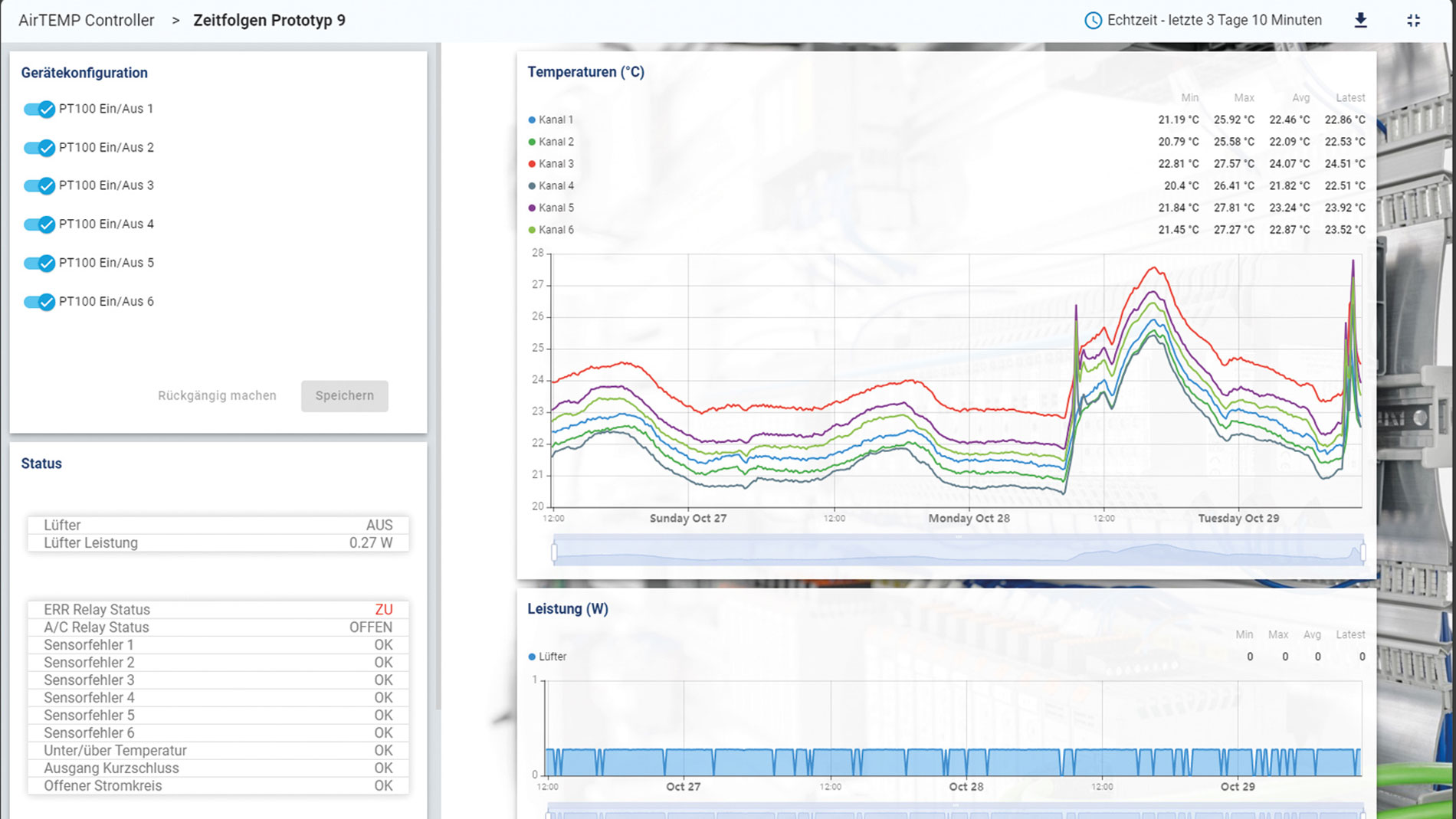
Ein weiteres Praxisbeispiel für die Vernetzung von IT und OT findet sich im Schaltschrankmonitoring: Die Friedrich Lütze GmbH hat mit dem Airtemp Controller und Airtemp Monitor eine IoT-Lösung entwickelt, die die thermische Überwachung von Schaltschränken revolutioniert. Das System kombiniert Sensortechnik mit Cloud-Anbindung, um Temperaturdaten in Echtzeit zu erfassen und auszuwerten. Der Airtemp Controller steuert dabei nicht nur die Lüfter zur Kühlung, sondern bietet über einen Relaisausgang auch direkte Schnittstellen zu Klimageräten. Die Besonderheit liegt in der Live-Überwachung via Airtemp Monitor – einem cloudbasierten Dashboard, das Betriebsverantwortlichen remote Zugriff auf die thermischen Prozesse ermöglicht. Die Integration in das bestehende Airstream Verdrahtungssystem zeigt, wie OT-orientierte Infrastruktur durch IT-Komponenten erweitert werden kann: Die rückseitig verbauten Airblower-Ventilatoren werden durch die IoT-Funktionalität intelligent vernetzt, wobei die Daten nicht nur der Prozessoptimierung dienen, sondern auch Energieeffizienzanalysen ermöglichen. Pilotprojekte demonstrieren, dass sich durch diese Form des Condition Monitorings die Betriebssicherheit erhöht, während gleichzeitig CO₂-Emissionen und Energiekosten transparent überwacht werden können. Die Lösung nutzt standardisierte Industrieprotokolle und lässt sich nahtlos in übergeordnete IIoT-Plattformen integrieren – ein Schlüsselaspekt für die Skalierbarkeit solcher Systeme.
Durch den Einsatz bildbasierter Analysemethoden erfahren Condition Monitoring und Predictive Maintenance eine erhebliche Erweiterung: Das Fraunhofer ITWM demonstriert dies im Projekt »Re(Pro)³«, das klassische Sensordaten mit maschineller Bildverarbeitung kombiniert. Der Ansatz integriert zeitliche Veränderungen von Produktqualitäten und Prozessparametern, die durch Verschleiß oder Fehlkonfigurationen entstehen. Dabei analysieren Algorithmen nicht nur Oberflächendefekte wie Kratzer oder Unregelmäßigkeiten, sondern korrelieren diese mit Maschinendaten wie Vibrationen oder Temperaturen. Dieser duale Blick ermöglicht es, Muster im Qualitätsverlauf frühzeitig zu erkennen – etwa wenn leichte Abweichungen in der Produktoberfläche auf beginnenden Werkzeugverschleiß hinweisen. Durch virtuelle Inspektionsplanung und Machine-Learning-Modelle prognostiziert das System, wann Toleranzgrenzen überschritten werden, und leitet daraus optimale Wartungszeitpunkte ab. In der Praxis reduziert dies Ausschussraten um bis zu 25 Prozent, wie Anwendungen in der Textil- und Kunststoffindustrie zeigen. Gleichzeitig entsteht ein softwarebasiertes Framework, das Produktionsdatenströme mit Qualitätsmerkmalen verknüpft und so die Grundlage für selbstoptimierende Produktionsprozesse schafft.
Gerade diese Verbindung von klassischer Sensorik, KI-gestützter Bildverarbeitung und datenbasierter Prozesssteuerung verdeutlicht, wie umfassend die Digitalisierung die industrielle Instandhaltung transformiert. Sie eröffnet neue Möglichkeiten, Fehlerursachen präziser zu identifizieren, Ressourcen gezielter einzusetzen und Produktionsprozesse nachhaltiger zu gestalten. Condition Monitoring und Predictive Maintenance sind damit Treiber der digitalen Transformation und der Vernetzung von IT und OT in der Industrie. <hjs>
Einrichtung von Alerts und Abruf der relevanten Daten für das Condition Monitoring über das Dashboard AirTEMP Monitor. (Bild: Friedrich Lütze GmbH)