Die Antriebstechnik steht vor der Herausforderung, trotz steigender Energiepreise, komplexer werdender Produktionsanforderungen und Nachhaltigkeitsziele höhere Wirkungsgrade zu erzielen. Künstliche Intelligenz (KI) kann hier als Gamechanger eingesetzt werden, der nicht nur Einsparpotenziale erschließt, sondern auch völlig neue Optimierungsansätze ermöglicht. Durch die Fähigkeit, Echtzeitdaten zu analysieren und prädiktive Entscheidungen zu treffen, durchdringt KI alle Phasen des Antriebslebenszyklus – von der Entwicklung über den Betrieb bis zur Wartung.
Im Kern revolutioniert KI die Effizienz, indem sie Sensordaten aus Antriebskomponenten kontinuierlich auswertet, Ineffizienzen identifiziert und Betriebsparameter dynamisch anpasst. Dieser Paradigmenwechsel von reaktiver zu prädiktiver Steuerung reduziert Energieverluste um bis zu 20 % und verlängert die Lebensdauer von Motoren um 30 bis 40 %. Ein zentraler Mechanismus ist die KI-gestützte Lastprofiloptimierung: Algorithmen gleichen Drehmomentanforderungen mit dem aktuellen Netzlastzustand ab, glätten Lastspitzen und vermeiden Teillastbetrieb – ein bisher unterschätzter Energiefresser.
Beispielhafte KI in der Antriebstechnik
Ein KI-Projekt zur Antriebs-Optimierung ist beispielsweise die Electrix AI des Herstellers WSCAD GmbH, die auf der Messe SPS 2024 vorgestellt wurde: Die E-CAD-Software integriert lernfähige Algorithmen, die historische Projektdaten mit physikalischen Simulationsmodellen verknüpfen, um beispielsweise Antriebsstränge automatisch auszulegen. In der Praxis verkürzt dies die Entwicklungszeit elektrischer Antriebe um 40 %, während gleichzeitig der Kupferbedarf in Wicklungen durch optimierte Leiterquerschnitte um 15 % sinkt. Ein Automobilzulieferer testet aktuell die automatische Generierung von Schaltplänen, die bisher 70 % der Engineering-Zeit beanspruchte.
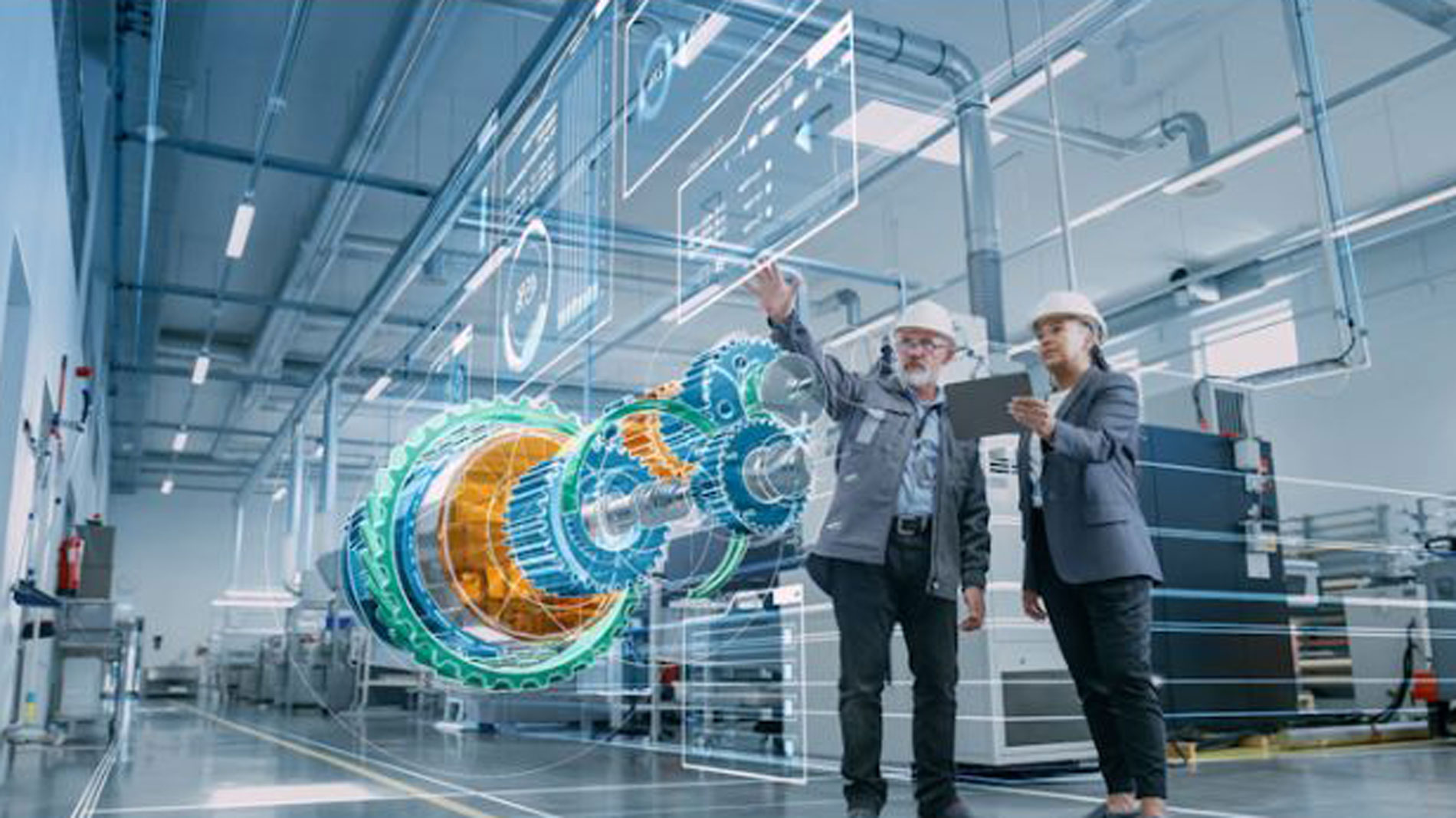
Weitere prägende Entwicklungen, die den Einsatz von KI in der Antriebstechnik vorantreiben, sind etwa das BMWK-geförderte Projekt Antrieb 4.0, das die Standardisierung von Schnittstellen und Datenformaten zum Ziel hat. Seit November 2024 ermöglicht ein Gaia-X-kompatibler Datenraum die herstellerübergreifende Vernetzung von Antrieben. KI-Algorithmen analysieren hier aggregierte Betriebsdaten aus 12.000 Antriebssystemen, um branchenweite Benchmarks für Energieeffizienz zu erstellen. Ein Demonstrator der TU Darmstadt zeigt, wie durch diesen Ansatz Überdimensionierungen bei Getrieben um 50 % reduziert werden – ein Effekt, der global jährlich 8,4 Mio. Tonnen Stahl einsparen könnte.
Initiativen wie Antrieb 4.0 ermöglichen durch gemeinsame Datenräume und KI-Methoden eine herstellerübergreifende, intelligente Optimierung und Vernetzung von Antriebssystemen. Bild: ZVEI
Generative KI-Modelle für automatisierten Antriebsentwurf
Parallel dazu fördert Horizon Europe, das Rahmenprogramm der Europäischen Union für Forschung und Innovation, seit Januar 2025 generative KI-Modelle, die multimodale Daten wie CAD-Skizzen, Schwingungsspektren und Thermografiedaten für den automatisierten Antriebsentwurf nutzen. Ergänzt wird diese Entwicklung durch neuartige Lösungen wie den Nvidia Jetson Orin, einem Developer Kit für AI, Robotik und Antriebe, das seit Ende 2024 dezentrale Signalverarbeitung direkt im Frequenzumrichter ermöglicht. Diese Edge-Lösungen reduzieren Latenzzeiten bei der Regelung von Servomotoren auf unter 50 Mikrosekunden, was Hochpräzisionsanwendungen wie Robotik oder CNC-Fräsen revolutioniert.
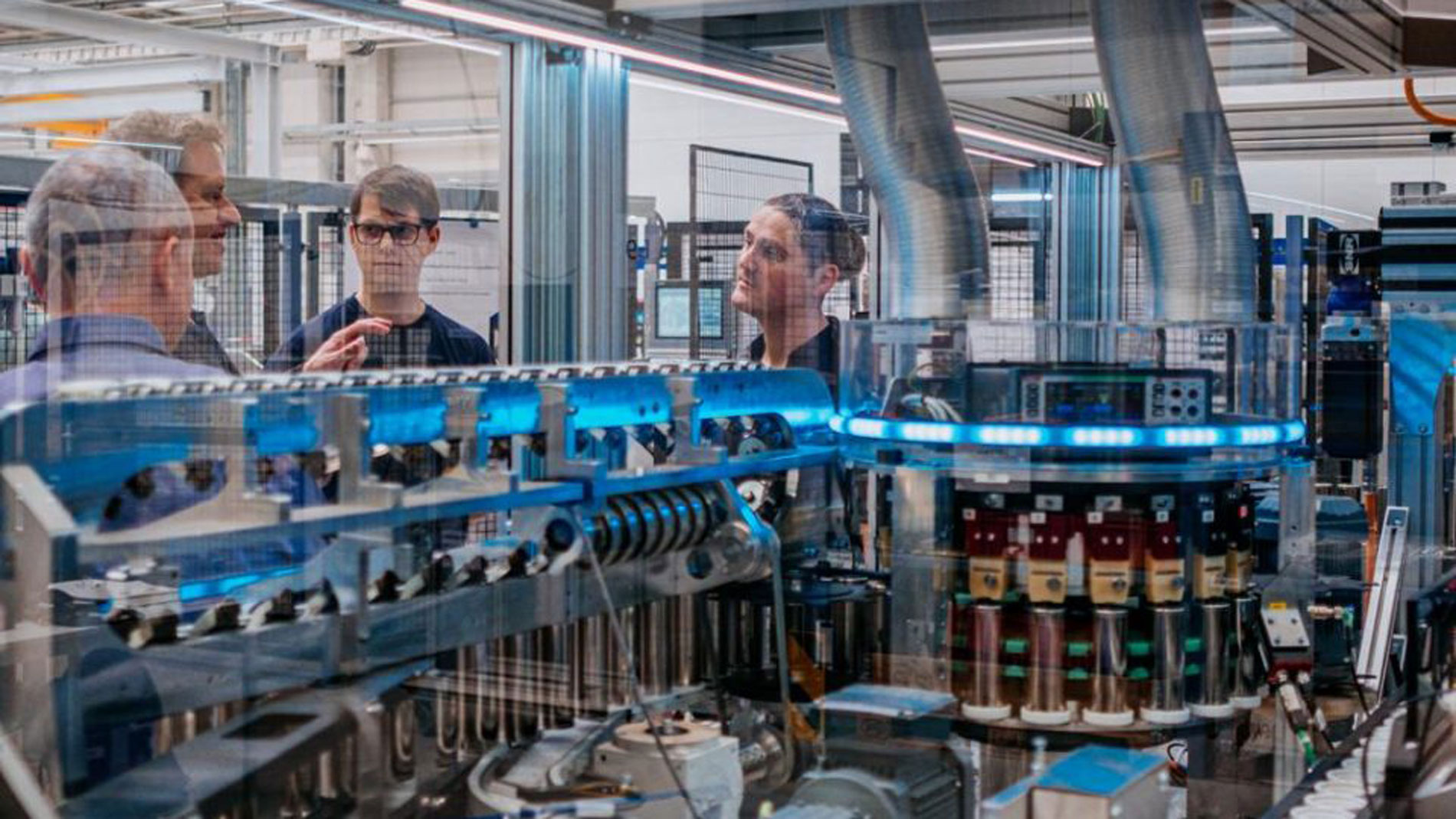
Ein weiteres Beispiel für die erfolgreiche Nutzung von KI in der Automatisierungs- und Antriebstechnik liefert die Partnerschaft zwischen Microsoft und Siemens mit dem Siemens Industrial Copilot. Dieser cloudbasierte Dienst nutzt Azure Open AI, um Maschinenvisualisierungen in 30 Sekunden zu generieren und angepassten PLC-Code bereitzustellen, der manuelle Nacharbeiten um 80 % reduziert. In einer Pilotanwendung bei Thyssenkrupp Automation Engineering sanken Stillstandszeiten durch prädiktive Fehlererkennung um 30 %, während der Energieverbrauch vernetzter Servomotoren um 12 % zurückging. Der Copilot trainiert sich kontinuierlich anhand von Betriebsdaten aus über 100 Kunden weiter, was die Genauigkeit der Vorhersagemodelle monatlich um 5 bis 7 % steigert.
Thyssenkrupp Automation Engineering setzt den KI-getriebenen Siemens Industrial Copilot auf Basis von Microsoft Azure OpenAI ein, um Stillstandszeiten und Energieverbrauch vernetzter Servomotoren erheblich zu reduzieren. Bild: Thyssenkrupp Automation Engineering.
KI als Treiber der künftigen Antriebsgeneration
Für die Zukunft zeichnen sich drei zentrale Trends ab, die KI als Treiber der nächsten Antriebsgeneration weiter etablieren werden. Machine Learning wird in Kürze Antriebe ermöglichen, die sich autonom an wechselnde Umgebungen anpassen – etwa an schwankende Netzspannungen oder Verschleißzustände. Projekte des BMBF kombinieren zudem Quantensensoren mit KI, um Schwingungsmuster in Antrieben mit 99,9 % Genauigkeit zu analysieren. Gleichzeitig arbeitet der VDE an einer Ethical-AI-Zertifizierung, die KI-Systeme hinsichtlich Transparenz, Energieeffizienz und Datensouveränität bewertet.
Herausforderungen bleiben die Harmonisierung von Datenstandards und die Skalierung von Pilotprojekten. Initiativen wie Antrieb 4.0 schaffen hier Abhilfe, indem sie offene Referenzarchitekturen bereitstellen. Und eine Vorhersage kann sicher gemacht werden: Mit der zunehmenden Verbreitung von KI-Tools wird die Antriebstechnik die nächsten Jahre einen Quantensprung in Effizienz und Nachhaltigkeit vollziehen. (hjs)