Die europäische Fertigungsindustrie steht vor einer doppelten Herausforderung: Sie muss ihre globale Wettbewerbsfähigkeit sichern und die digitale und nachhaltige Transformation vorantreiben. Eine Initiative prägt dabei die Strategie – Manufacturing-X. Sie zielt darauf ab, die industrielle Datenökonomie durch standardisierte, sichere und souveräne Datennutzung zu revolutionieren.
Manufacturing-X ist eine branchenübergreifende Initiative, die einen offenen Datenraum für Industrie 4.0 etabliert. Dieser ermöglicht es Unternehmen, Daten entlang der Wertschöpfungskette zu teilen – von der Lieferantenkommunikation bis zum CO₂-Fußabdruck-Management –, ohne die Hoheit über sensible Informationen zu verlieren. Kern ist die Schaffung interoperabler Ökosysteme, die auf offenen Standards wie OPC UA, MQTT oder der Asset Administration Shell (AAS) basieren. Gerade für die Antriebstechnik bedeutet dies, dass Antriebsdaten standardisiert, sicher und herstellerübergreifend genutzt werden können, was Predictive Maintenance, Energieoptimierung und eine schnellere Integration neuer Antriebslösungen in vernetzte Produktionsumgebungen ermöglicht.
Kongress zeigt Mehrwert von Manufacturing-X
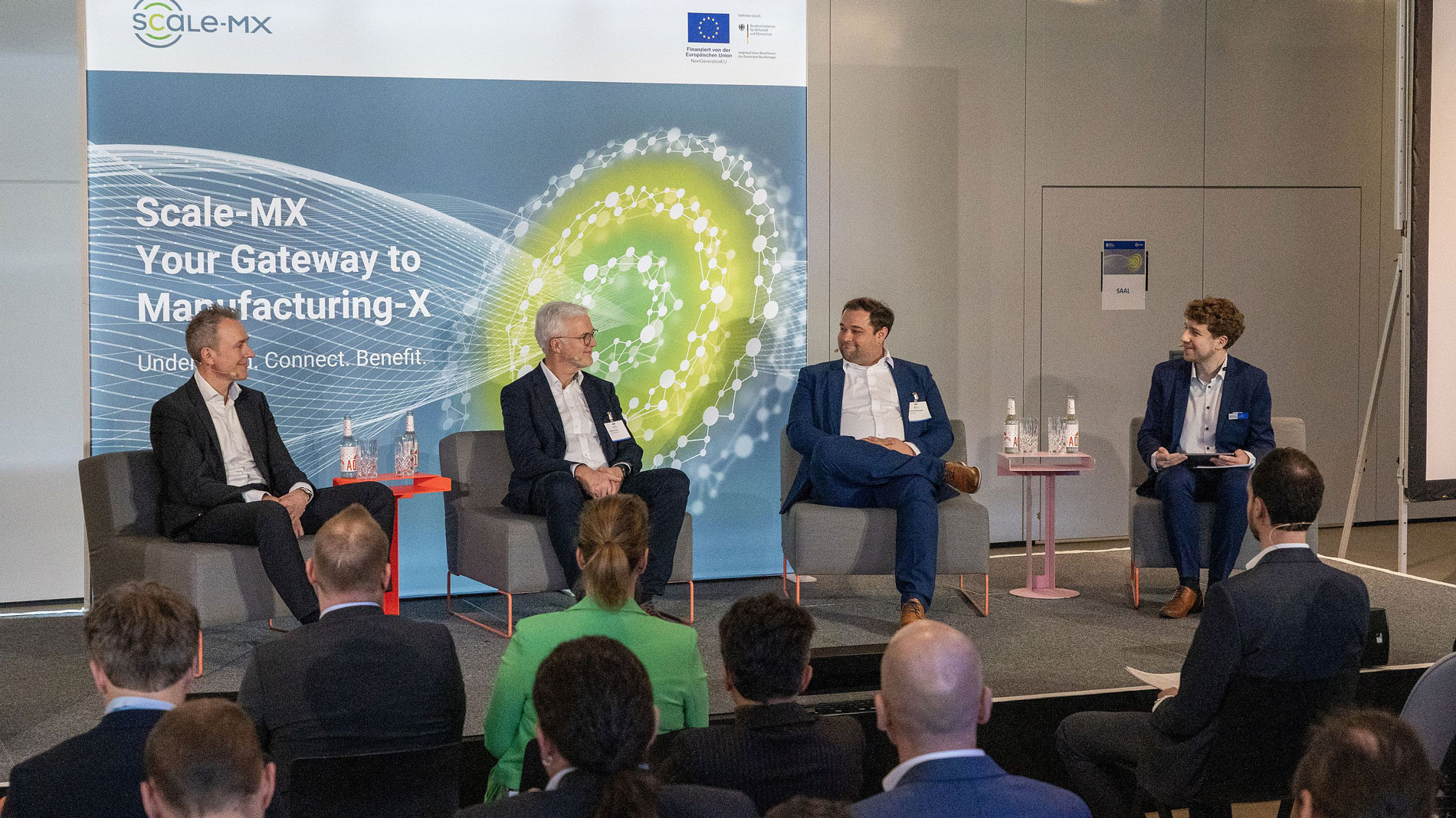
Scale-MX ergänzt dies als Transferinitiative, die den Praxiseinsatz beschleunigt. Sie unterstützt insbesondere KMU durch Leitfäden, Best Practices und skalierbare Technologien, um Datenräume branchenübergreifend nutzbar zu machen. Einen praxisnahen Einblick bot der erste Scale-MX Kongress in München, veranstaltet von Bayern Innovativ, auf dem rund 300 Teilnehmende konkrete Anwendungen und Mehrwerte von Manufacturing-X erleben konnten. In Vorträgen, Ausstellungen und Use Cases – etwa zum digitalisierten Asset Management mit Antrieb 4.0 – wurde gezeigt, wie industrielle Datenräume in der Praxis funktionieren und wie Unternehmen durch offenen Datenaustausch Effizienz und Transparenz steigern können.
Der erste Scale-MX Kongress bot sowohl Einsteigern als auch erfahrenen Anwendern einen wertvollen Überblick über industrielle Datenräume und zahlreiche Möglichkeiten zum Austausch mit Projekten der Manufacturing-X Initiative. Bild: Bayern Innovativ GmbH
Datenräume bilden die technologische Basis dieser Initiativen. Sie sind föderierte Infrastrukturen, die einen sicheren, regelbasierten Datenaustausch zwischen Unternehmen ermöglichen. Im Gegensatz zu geschlossenen Plattformen gewährleisten sie digitale Souveränität: Jeder Teilnehmer behält die Kontrolle über seine Daten und entscheidet, wer welche Informationen zu welchen Bedingungen nutzen darf. Für die europäische Industrie ist dies existenziell, um Abhängigkeiten von außereuropäischen Tech-Giganten zu vermeiden und gleichzeitig resiliente Lieferketten aufzubauen. Ein Beispiel ist der Einsatz in der Antriebstechnik: Durch herstellerübergreifende Datenräume können Wartungsintervalle optimiert oder Energieverbräuche transparent gemacht werden – ohne dass Betriebsgeheimnisse preisgegeben werden
Anforderungen an moderne Antriebstechnologien
Um in Manufacturing-X-Netzwerke integriert zu werden, müssen Antriebssysteme vier zentrale Kriterien erfüllen:
- Interoperabilität durch Standardisierung: Antriebe müssen Schnittstellen unterstützen, die einen nahtlosen Datenaustausch ermöglichen. Dazu zählen maschinenlesbare Beschreibungsformate wie die AAS, Kommunikationsprotokolle wie OPC UA oder MQTT sowie semantische Standards für Metadaten. Projekte wie Antrieb 4.0 zeigen, wie Verwaltungsschalen (Digital Twins) Maschinendaten herstellerunabhängig erfassbar machen.
- IIoT- und KI-Fähigkeit: Moderne Antriebe benötigen Sensorik und Edge-Computing-Kapazitäten, um Zustandsdaten (Vibration, Temperatur, Leistungsaufnahme) in Echtzeit zu analysieren. KI-Algorithmen nutzen diese Daten für Predictive Maintenance oder adaptive Regelungen – etwa zur Energiereduktion bei Lastspitzen.
- Cybersecurity by Design: Da vernetzte Antriebe Teil kritischer Infrastrukturen sind, müssen sie Schutzmechanismen wie Ende-zu-Ende-Verschlüsselung, Zugriffskontrollen und regelmäßige Sicherheitsupdates integrieren.
- Nachhaltigkeitsorientierung: Energieeffizienz allein reicht nicht mehr. Antriebe müssen Daten liefern, die eine CO₂-Bilanzierung über den gesamten Lebenszyklus ermöglichen – von der Materialbeschaffung bis zum Recycling.
Antriebslösungen im Datenraum
Anbieter wie Siemens, Beckhoff, Bosch Rexroth und SEW-Eurodrive setzen bereits auf Manufacturing-X-kompatible Architekturen. Siemens integriert beispielsweise AAS-basierte Digital Twins in seine Sinamics-Antriebe, um Instandhaltungsdaten in föderierten Datenräumen bereitzustellen. Dadurch können Anwender Wartungsintervalle präzise vorhersagen, ungeplante Stillstände reduzieren und gleichzeitig durch datenbasierte Optimierung der Antriebsparameter bis zu 20 % Energie einsparen – alles in einem herstellerübergreifend interoperablen Manufacturing-X-Ökosystem.
Beckhoff treibt mit der Twincat-Cloud die Anbindung an industrielle Datenräume voran. Dadurch können Antriebssysteme in Echtzeit über die Cloud überwacht, KI-gestützte Lastprofile optimiert und Predictive-Maintenance-Konzepte branchenübergreifend umgesetzt werden – bei gleichzeitig sicherer Datenhoheit und reduziertem Engineering-Aufwand durch direkte Integration in Manufacturing-X-Ökosysteme.
Wegbereiter der Industrie von morgen
Bosch Rexroth setzt mit der offenen Automatisierungsplattform Ctrlx Automation auf eine Manufacturing-X-kompatible Architektur, bei der elektrische Antriebe, Steuerungen und innovative Softwarelösungen über offene Standards wie OPC UA und App-Technologie nahtlos in industrielle Datenräume eingebunden werden können; so lassen sich Antriebsdaten flexibel, sicher und herstellerübergreifend für vorausschauende Wartung, Energieoptimierung und die Integration in digitale Wertschöpfungsketten nutzen.
SEW-Eurodrive verfolgt mit der modularen Getriebe- und Antriebstechnik der Generation X.e sowie mit intelligenten Umrichtern und digitalen Schnittstellen wie Movilink DDI einen konsequenten Ansatz zur Vernetzung und Datenintegration; die Antriebe sind so ausgelegt, dass sie über Feldbus- und Ethernet-basierte Kommunikation sowie umfangreiche Sensorik und Diagnosetools optimal in Manufacturing-X-Architekturen eingebunden werden können und damit eine durchgängige, interoperable Nutzung von Betriebs- und Zustandsdaten im Datenraum ermöglichen
Open-Source-Tools erleichtern Überführung in Datenräume
Für KMU bieten Projekte wie Antrieb 4.0 konkrete Umsetzungshilfen: Der vom Verband ZVEI geleitete Forschungsverbund entwickelte Open-Source-Tools, um Antriebsdaten in standardisierte Verwaltungsschalen zu überführen. Damit wird es möglich, Antriebssysteme herstellerübergreifend und interoperabel in föderierte Datenräume einzubinden, wie sie im Rahmen von Manufacturing-X entstehen, sodass ein sicherer, transparenter und effizienter Datenaustausch über Unternehmensgrenzen hinweg realisiert werden kann.
Auch Start-ups wie Cybus liefern Middleware-Lösungen, die Legacy-Antriebe nachträglich in Datenräume einbinden. Das heißt, mit diesen Softwarelösungen können ältere, ursprünglich nicht-vernetzte Antriebssysteme über standardisierte Schnittstellen und Protokolle wie OPC UA oder MQTT mit modernen digitalen Plattformen verbunden werden. So werden Betriebs- und Sensordaten gesammelt, vereinheitlicht und sicher bereitgestellt, wodurch auch Bestandsanlagen in Manufacturing-X-Ökosystemen für Analysen, Optimierungen und digitale Services genutzt werden können.
Manufacturing-X und Scale-MX sind also keine theoretischen Konzepte, sondern praktische Hebel für die industrielle Zukunft Europas. Für Automatisierer bedeutet dies: Antriebstechnik muss als vernetzter Datenlieferant gedacht werden – sicher, standardisiert und nachhaltig. Nur so entsteht eine resiliente, KI-gestützte Fertigung, die globalen Herausforderungen standhält. (hjs)